A machine operator places pieces of black and white plastic on a long conveyor belt. Out at the other end comes finely ground plastic, which is then melted down and given a new lease of life. At Rani Plast, everything comes full circle.
Production at its Terjärv factory is under a closed-loop system. All plastic waste and waste material from production is recycled into new products. But that’s not all. A new re-granulation facility has recently been commissioned, to further increase the factory’s plastic recycling capacity. Mats Albäck is Rani Plast’s Sustainability and Development Director. He summarises the position as follows.
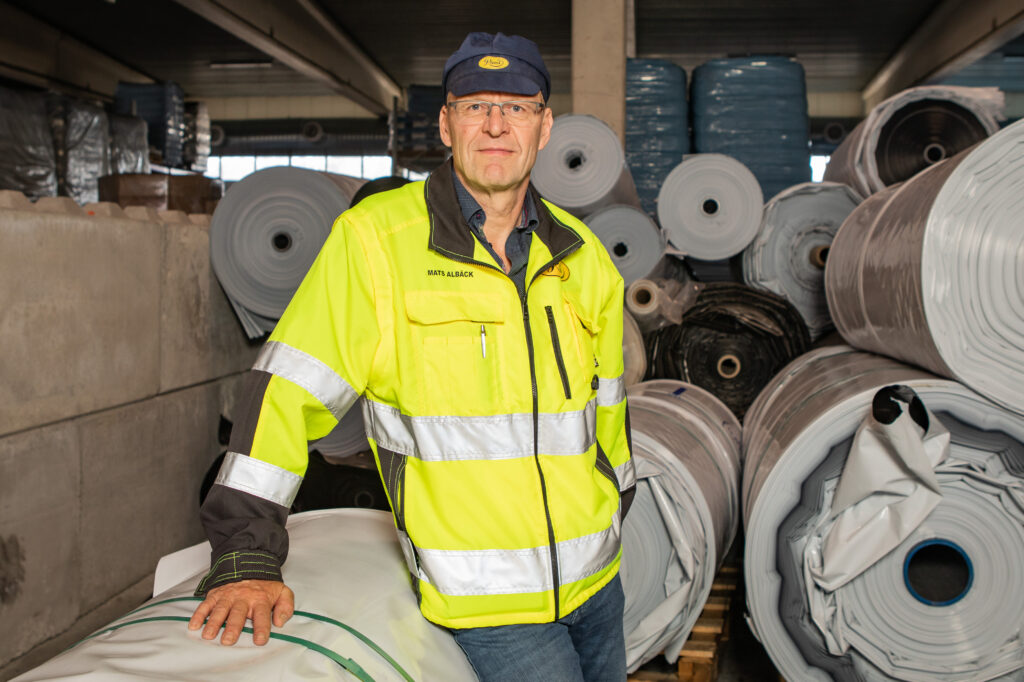
– Today, all our products are 100 percent recyclable, and we aim to reach around 25 percent integration of recycled material in our products within the next year. Some of those products will contain a higher percentage of recycled material than others.
The new facility will provide an additional capacity of around 8,000 tonnes of plastic granulates per year. It is further evidence of the company’s long-term commitment to more sustainable production.
The efficient usage of material has been a part of the company’s business strategy since its inception, for financial reasons. But the reasoning has shifted to a circular frame of mind, according to Mats Albäck. He adds that as a producer, Rani Plast has a great responsibility towards the industry, and can pave the way for other companies.
We must develop products that can be recycled
– Circular thinking starts in the product development and design process, he says. We must develop products that can be recycled, and products that can be made from recycled materials. In practice, this means working closely with our raw materials suppliers and customers. Because we have ample experience of working in a circular way, we are often the ones able to devise solutions. Recycling our own materials is easy; the challenge lies in processing others’ plastic waste.
Plastic waste from consumers must be sorted and treated, and this is quite an extensive process. Rani Plast lacks a suitable facility. The same can be said for dealing with agricultural plastics, which contain, for example, soil and feed residues. These types of raw materials are sourced externally, already re-granulated.
Plastic is only a part of our personal carbon footprint
For Rani Plast, sustainability includes a responsibility to the environment. The factory’s carbon footprint has been carefully monitored for several years now. As plastics are melted and cooled, the industry is generally very energy intensive.
– We have switched to zero-emission electricity and have installed solar panels at the new facility. But we can do more. One thing is to replace our forklifts with new biogas-powered variants. Further measures we can take include using biogas in printing, and electric vehicles.
Mats Albäck also points out that plastics have been given an unfair reputation.
– Plastic is a superior packaging material if it is used correctly and for the right purpose, such as the packaging of food items.
In fact, plastic is only a small part of our personal carbon footprint. He points to a study showing that plastic accounts for just 0.6 percent of the average European consumer’s carbon footprint. Heating accounts for 18 percent, cars and food for 14 percent each, and the biggest culprit is consumption, at 25 percent.
– If you ask me, I think it’s good to reflect on our own consumer habits from time to time, he says.
Rani Plast – About us
Rani Plast specialises in the production of packaging film for industrial and agricultural customers. The company has deep roots in its hometown of Terjärv and is part of the family-owned Rani Group. The group owns nine factories in five countries, has around 1,000 employees, an annual turnover of over 300 million euro, and exports products to 50 countries.
Read our other Sustainability stories
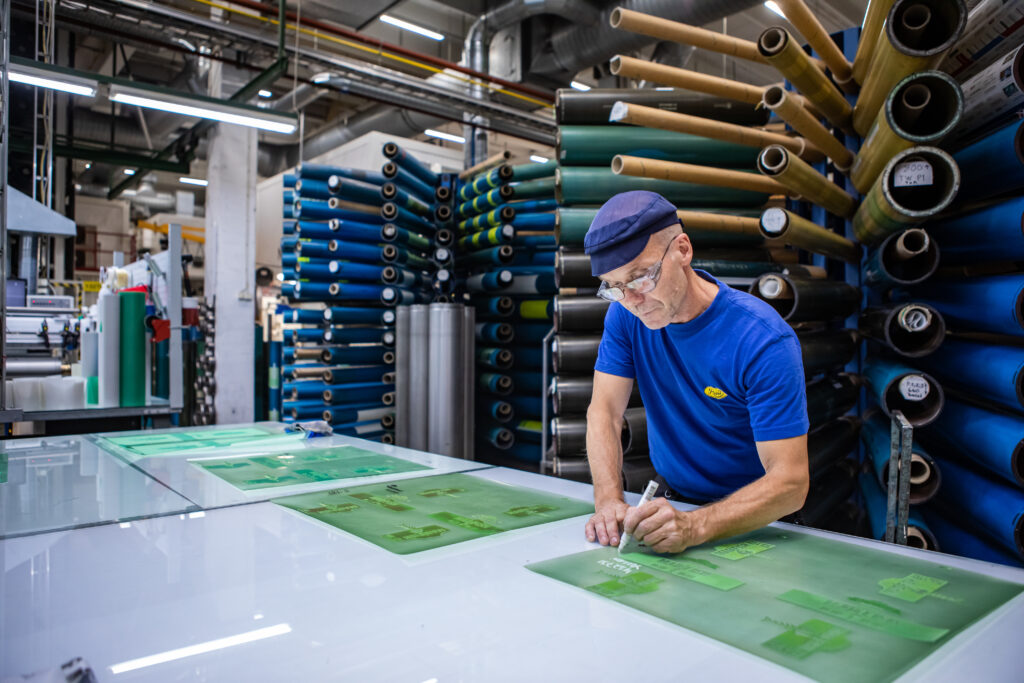
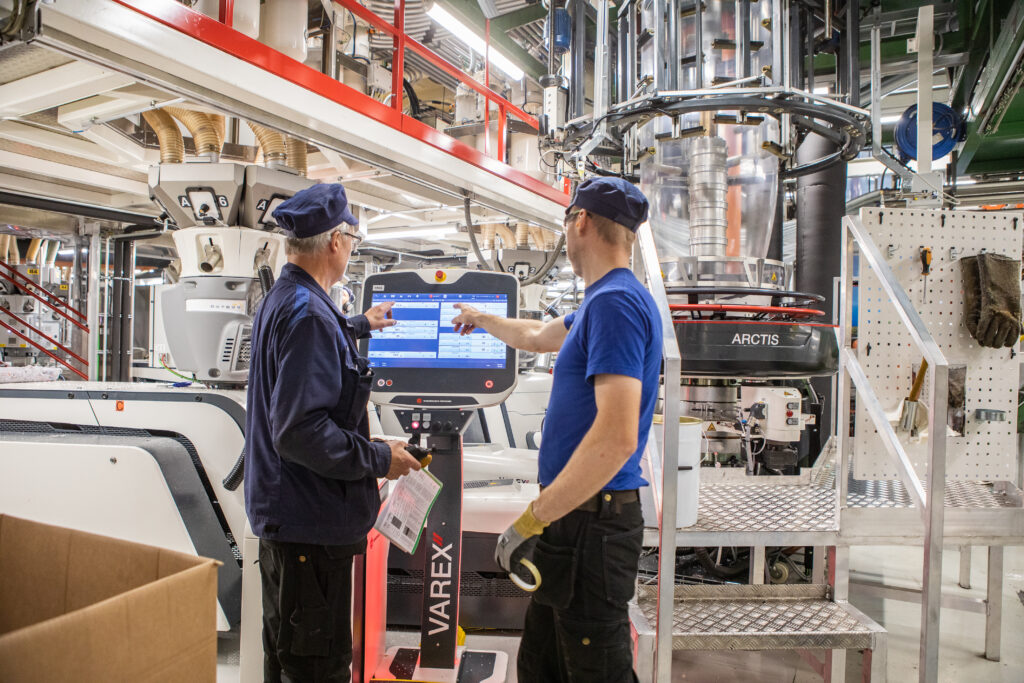
This series of articles have been produced within the CIT-project (Circular Insights and Transition) which is financed by the European Regional Development Fund, The Council of Ostrobothnia together with all Development companies in Ostrobothnia.
