Solving’s automated guided vehicles (AGVs) and movers handle everything from rockets to trucks to canisters of spent nuclear fuel. Its machinery is built to last, but that doesn’t mean the company isn’t looking for ways to make manufacturing more sustainable.
Growth is an important common factor among companies in the Jakobstad region. Local entrepreneurs demonstrate good business sense, and several of them have achieved global leadership. But one area in which regional businesses do not excel is telling others about their achievements. However, at Solving this might be about to change.
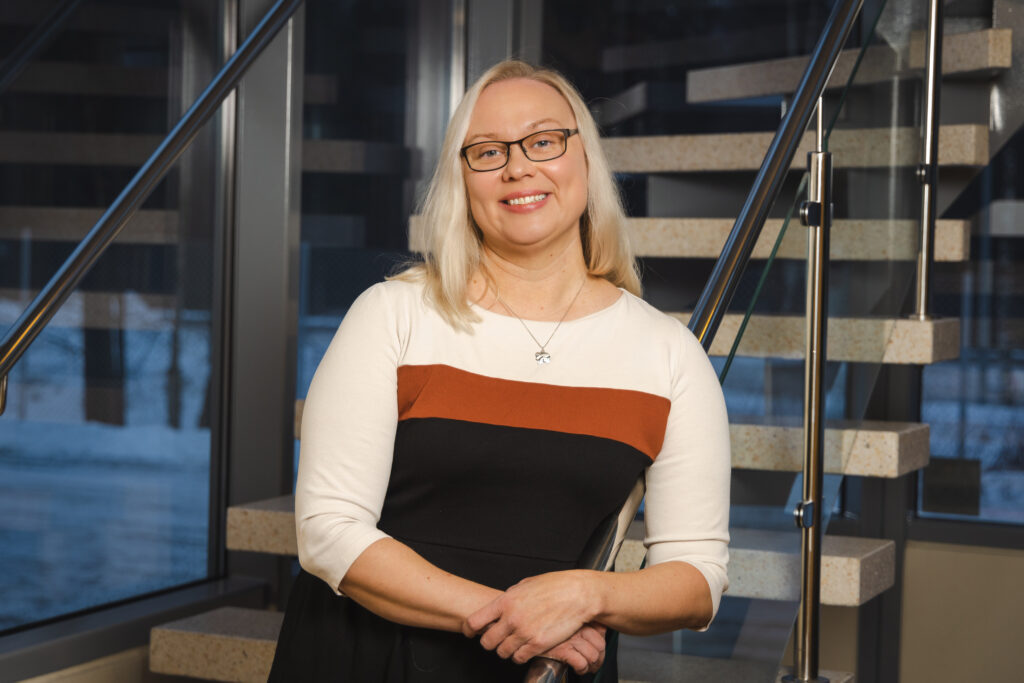
– We’ve decided to get better at talking about our long-term efforts to meet our customers’ demands for transparency in manufacturing, says Quality Manager Jenny Valo.
The green transition is progressing well for her regional colleagues, and she is pleased to be a part of this network. Although Solving is a global company, it attaches great importance to its local customers and suppliers. A number of regional businesses use Solving’s movers and AGVs in their operations, and Solving, in turn, has a preference for local suppliers.
– Many local businesses have set the bar high in terms of their partners and how they operate, says Jenny Valo. The co-operation between benchmark companies helps spread knowledge throughout the region.
New production facilities is in the pipeline
At the moment there is hardly an inch of free space in Solving’s assembly hall. It’s a hive of industry, with a big order of AGVs for Swedish truck giant Scania and two yellow custom models for Posiva, a Finnish company that specialises in the final disposal of spent nuclear fuel.
– These are probably the world’s first automated guided vehicles built for that purpose, and we hope their delivery will result in further, similar projects.
The AGVs are being built to carry nuclear waste canisters that will be placed on elevators and transported to a repository, hundreds of metres underground.
The utmost degree of transparency and precise documentation were requisites for the Posiva order. Jenny Valo says the process was a real eye-opener for Solving.
– This is the direction we are now taking.
But the company is currently facing more pressing challenges. The business has grown so fast in recent years that it has literally outgrown its premises. The construction of new production facilities is in the pipeline, and she expects sustainability criteria to be taken into account.
– Heating and travel are two of our biggest challenges. Our programmers must be on-site during the commissioning of our equipment. This work cannot be done remotely. We have about ten programmers who each travel up to 150 days per year.
Sustainability and products with long lifespan are in focus
Solving’s transition towards more sustainable production is in progress, and Jenny Valo is currently evaluating its carbon footprint. The warehouse, however, is one thing she is already proud to talk about. Solving has reduced waste by implementing a system where components are ordered as needed per project. The warehouse’s shelved boxes contain exactly the parts required to build a particular AGV or mover; no more, no less.
The 5S Lean Manufacturing approach has long been adopted in the assembly hall, as has a policy to encourage reuse.
– To start with, our AGVs are built to last for decades, she says. We’ve also strengthened our after-sales service. We accept our machines, and those of our competitors, for repairs and upgrades. Our supply of spare parts and repair services play an important role in our sustainability efforts.
Solving – About us
NASA, Scania, and Posiva: Solving’s customers include the world’s biggest players. Solving manufactures handling systems based on air bearings or wheels, permitting heavy industrial loads to be handled efficiently and safely. Its AGVs and movers are highly automated. Solving has its facilities in Sandsund, Pedersöre and is part of the Solving Group. The company exports its products to 60 countries.
www.solving.com
Read our other Sustainability stories
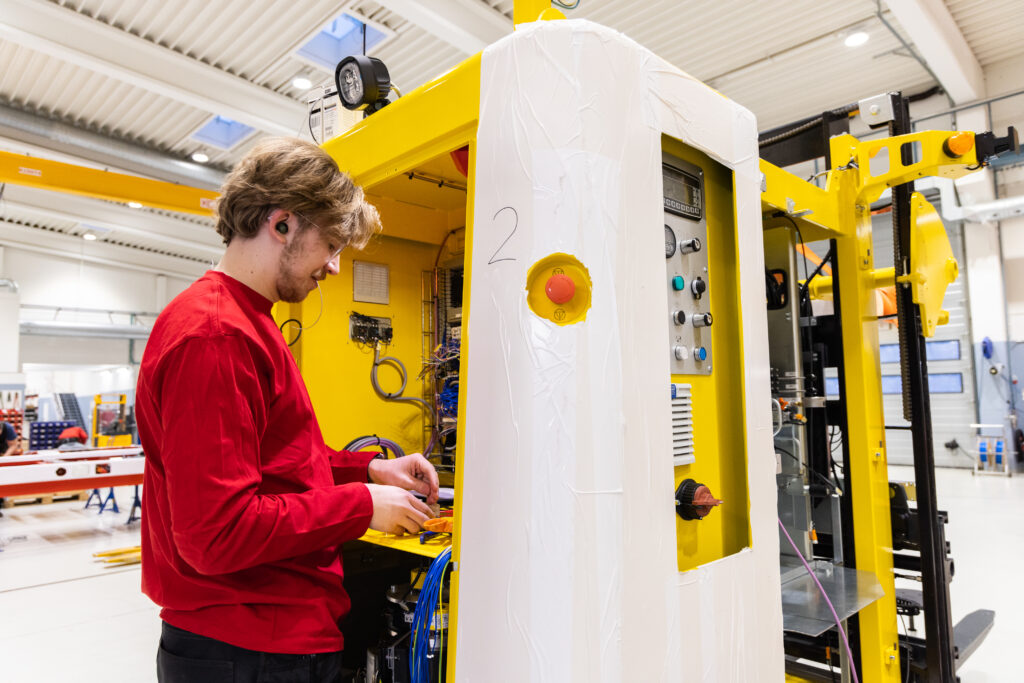

This series of articles have been produced within the CIT-project (Circular Insights and Transition) which is financed by the European Regional Development Fund, The Council of Ostrobothnia together with all Development companies in Ostrobothnia.
